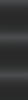
Proven Flooring Solutions
Following step by step recipes for floor coatings that have been proven by Ideal Polymers to give you the best results is the only way to get ahead faster. Having a reliable source built on 30 years of field experience, knowledge and data, providing you real time answers and suggestions to your questions.

ColorFloor
ColorFloor Epoxy System-
This is a 3 layer epoxy and urethane resinous flooring system. The following scope of work is to install a solid color epoxy and urethane resinous flooring system using the methods and materials listed below:
1) ColorFloor Verify Measurements-
(Contractor Company Name) will verify the dimensions of the work area, and all details provided by the customer to create this proposal. Any additional items found to be needed or adjustments to be made, can be done as a Change Order with the approval of you the Customer.
Preparation Services
1) ColorFloor Coverings Removal/Demo-
If applicable remove the existing floor coverings and haul away: Tile or Carpet. Please note that if additional layers of floor coverings are found to be underneath what can be seen, a Change Order for the added cost must be made and will be based on the type and amount of additional removal needed.
2) ColorFloor Moisture Test-
This is a test to determine the level of moisture vapor that is naturally evaporating and outgassing from your existing concrete floor. This test does not determine any structural issues, plumbing issues, or the like. Being that all concrete floors are different, the standard acceptable results for the epoxy layers are 3 pounds of moisture per an average 1,000 square feet area, over a 24 hour period. If the results of the moisture tests are higher than the acceptable results, then we recommend a moisture vapor barrier that is listed below.
3) ColorFloor Diamond Grind-
Use diamond grinders around edges and as needed to achieve profile in accordance with the International Concrete Repair Institute.
4) ColorFloor Shotblast-
A metal sand shot blaster used to achieve profile in accordance with International Concrete Repair Institute. Please note that some tooling marks from shot blasting may be visible within the coatings layers. Softer concrete surfaces may show more tooling marks than harder, newer concrete surfaces. As well, areas of weak surfaces may require additional patching, which is an unknown until after the shot blasting process has been completed. Areas that require large amounts of additional patching will require a Change Order with the approval of you the Customer. Vacuum thoroughly once desired profile is achieved.
Installation Services
1) ColorFloor Joint Fill-
Place backer rod into joints and install joint fill product to create a smoother surface and protect against collection water, ice, dirt and debris. Unfilled joints do not provide this protection. Note that the joints are at the surface edge in order to allow for expansion and contraction of the joint fill material.
2) ColorFloor Crack Fill -
Fill cracks in concrete with an epoxy patching compound. Cracks larger than 1/32" will be filled to help provide a smoother more professional appearance.
Please note that filling any crack does not create a structural repair. Epoxy creates a high-strength bond that reinforces the concrete rather than just covering the crack but does not guarantee to remediate a concrete slab that is moving, or has moisture pressure from underneath.
3) ColorFloor Patching-
Apply epoxy patching material to areas of concrete to reduce severity of depressions. Epoxy patching compounds are stronger than regular concrete repairs and ensure the substrate remains solid and stable under traffic and weight loads, as a properly prepped surface extends the durability and longevity of the epoxy coating.
4) ColorFloor Cove Base-
If purchased by the customer install an epoxy mortared cove base along the wall locations specified and at what height from the floor up the wall.
Epoxy cove bases are extremely durable in many commercial applications and help create more of a tub affect with its integral design with the floor. This helps with regular and heavy-duty cleaning processes and helps keep water from migrating under walls.
5) ColorFloor VaporStop-
If moisture test results are above the standard allowed by the coating material, a moisture vapor barrier is recommended. We will apply a special VaporStop coating to reduce amount of moisture that can outgas from the concrete slab and attack the coating system.
Please note that moisture vapor barriers do not protect against running water, drainage problems or the like. These coatings are intended to resist moisture vapor only and extend the life of the concrete floor.
6) ColorFloor Buffing/Sanding-
A rotating floor machine used to prep the surface for the next coating layer by buffing or sanding, which helps smooth out general dust and debris that naturally accumulates onto the wet epoxy layers between coats. Vacuum thoroughly once desired profile is achieved.
7) ColorFloor Epoxy Base Coat-
Apply 100% Solids epoxy base coat tinted in accordance with customer color information.
The epoxy base coat has excellent dwell time, rather than rapidly curing, which provides excellent penetration by seeping deep into the concrete pores, catalyzing inside the concrete and not just laying on top like paint coatings. Once cured, repeat step 6.
8) ColorFloor Epoxy Build Coat-
Apply a second layer of 100% epoxy, tinted in accordance with the customer color information.
The epoxy build coat helps create a thicker, stronger and smoother floor, which extends the life of the concrete coating system, is easier to clean, with a professional appearance. Once cured, repeat step 6.
9) ColorFloor Polyaspartic Top Coat-
Apply polyaspartic top coat tinted in accordance with customer color information.
The polyaspartic topcoat provides excellent resistance to many types of liquids, foods, animal waste, dirt, salt and more, and are highly resistant to UV light.
OR
9) ColorFloor Urethane Top Coat-
Apply Urethane coating tinted in accordance with customer color information.
-The High Wear Urethane is a very durable finish that is highly resistant to scratching. The appearance is also a low sheen with a slight surface texture.
-The Water Based Urethane uses water as the main solvent, with lower volatile organic compounds. It dries significantly faster than oil-based urethane, allowing for multiple coats in a single day. Typically dries clear, preserving the natural color.
-The Moisture Cure Urethane is a coating that hardens when it absorbs moisture from the air or a surface. It cures in cold weather, can handle higher heat temperatures than most epoxies, can be spray applied wet-on-wet, has short drying times, and can be used in high humidity and other challenging environments.
10) ColorFloor Traction Control-
If purchased by the customer, add aggregate for traction control in accordance with "System Layers and Colors" Information. Add aggregate to create traction for a better nonskid surface. We recommend traction on all floors, although any surface can be slippery when wet. Adding traction does not completely eliminate the possibility of slips and falls. We (Contractor Name) cannot be responsible for any injury.
11) ColorFloor Haul Trash-
Remove all related trash from the work area and dispose of into an offsite dumpster.
AND/OR
11) ColorFloor Trash Disposal-
All related trash will be bagged and disposed of into the jobsite dumpster provided by the Customer.
12) ColorFloor Discount-
Discount applied to the total of the floor coating system. No discount is applied to additional line items or Change Orders unless approved by (Contractor Name).
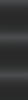

Broom Finish
Broom Finish System-
This is a concrete overlay technique where a broom is brushed across the wet surface to create a textured, slip resistant, and durable surface, commonly used for patios, walkways, and driveways. Applied using the methods and materials listed below:
1) Broom Finish Verify Measurements-
(Contractor Company Name) will verify the dimensions of the work area, and all details provided by the customer to create this proposal. Any additional items found to be needed or adjustments to be made, can be done as a Change Order with the approval of you the Customer.
Preparation Services
1) Broom Finish Power Wash-
Power wash the concrete surface.
2) Broom Finish Shotblast-
A metal sand shot blaster used to achieve profile in accordance with International Concrete Repair Institute. Please note that some tooling marks from shot blasting may be visible within the coatings layers. Softer concrete surfaces may show more tooling marks than harder, newer concrete surfaces. As well, areas of weak surfaces may require additional patching, which is an unknown until after the shot blasting process has been completed. Areas that require large amounts of additional patching will require a Change Order with the approval of you the Customer.
3) Broom Finish Diamond Grind-
Use diamond grinders around edges and as needed to achieve profile in accordance with the International Concrete Repair Institute. Vacuum thoroughly once desired profile is achieved.
4) Broom Finish Patching-
Apply patching material to areas of concrete to reduce severity of depressions. Unless measured, amount of patching material will be determined on-site and may result in a Change Order
Installation Services
1) Broom Finish Primer Coat-
Concrete primer to be applied before overlay.
2) Broom Finish Base Coat-
Trowel a base coat of overlay
3) Broom Finish Top Coat -
Trowel a top coat of concrete overlay. Apply an engineered concrete overlay in accordance with the "System Layers and Colors" Information
4) Broom Finish-
Apply a broom finish texture
5) Broom Finish Border-
If purchased by the customer, apply an Overlay border in accordance with the "System Layers and Colors" Information
6) Broom Finish Sealer-
Apply sealer to the overlay system in accordance with the "System Layers and Colors" Information
7) Broom Finish Traction-
If purchased by the customer, add aggregate for traction control in accordance with "System Layers and Colors" Information. Add aggregate to create traction for a better nonskid surface. We recommend traction on all floors, although any surface can be slippery when wet. Adding traction does not completely eliminate the possibility of slips and falls. We (Contractor Name) cannot be responsible for any injury.
9) Broom Finish Discount-
Discount applied to the total of the floor coating system. No discount is applied to additional line items or Change Orders unless approved by (Contractor Name).
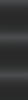

Clean & Seal
Clean & Seal System-
This is a process where concrete surfaces are thoroughly cleaned, prepared, and then sealed with a protective coating to enhance their durability, appearance, and resistance to staining and damage using the methods and materials listed below:
1) Clean & Seal Verify Measurements-
(Contractor Company Name) will verify the dimensions of the work area, and all details provided by the customer to create this proposal. Any additional items found to be needed or adjustments to be made, can be done as a Change Order with the approval of you the Customer.
Preparation Services
1) Clean & Seal Manual Clean-
Clean concrete surfaces with a Ph neutral cleaner and using mops, buckets and electric buffing equipment with scrubbing pads.
1) Clean & Seal Power Wash-
Power wash the concrete surface.
OR
1) Clean & Seal HOT Power Wash-
Power wash exterior concrete with hot power wash for a deeper more thorough clean.
Installation Services
1) Clean & Seal Sealing-
Apply color sealer to the concrete in accordance with the "System Layers and Colors" Information
2) Clean & Seal Traction-
If purchased by the customer, add aggregate for traction control in accordance with "System Layers and Colors" Information. Add aggregate to create traction for a better nonskid surface. We recommend traction on all floors, although any surface can be slippery when wet. Adding traction does not completely eliminate the possibility of slips and falls. We (Contractor Name) cannot be responsible for any injury.
3) Clean & Seal Haul Trash-
Remove all related trash from the work area and dispose of into an offsite dumpster.
OR
3) Clean & Seal Trash Disposal-
All related trash will be bagged and disposed of into the jobsite dumpster provided by the Customer.
4) Clean & Seal Discount-
Discount applied to the total of the floor coating system. No discount is applied to additional line items or Change Orders unless approved by (Contractor Name).
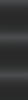

Color Seal
Color Seal System-
This is a method of applying a colored, protective sealer to concrete surfaces, enhancing their appearance and durability by providing a long-lasting, stain-resistant, and often UV-resistant finish. Used to protect and color concrete surfaces like patios, driveways, and pool decks using the methods and materials listed below:
1) Color Seal Verify Measurements-
(Contractor Company Name) will verify the dimensions of the work area, and all details provided by the customer to create this proposal. Any additional items found to be needed or adjustments to be made, can be done as a Change Order with the approval of you the Customer.
Preparation Services
1) Color Seal Manual Clean-
Clean concrete surfaces with a Ph neutral cleaner and using mops, buckets and electric buffing equipment with scrubbing pads.
1) Color Seal Power Wash-
Power wash the concrete surface.
OR
1) Color Seal HOT Power Wash-
Power wash exterior concrete with hot power wash for a deeper more thorough clean.
Installation Services
1) Color Seal Coating-
Apply color sealer to the concrete in accordance with the "System Layers and Colors" Information
2) Color Seal Traction-
If purchased by the customer, add aggregate for traction control in accordance with "System Layers and Colors" Information. Add aggregate to create traction for a better nonskid surface. We recommend traction on all floors, although any surface can be slippery when wet. Adding traction does not completely eliminate the possibility of slips and falls. We (Contractor Name) cannot be responsible for any injury.
3) Color Seal Haul Trash-
Remove all related trash from the work area and dispose of into an offsite dumpster.
OR
3) Color Seal Trash Disposal-
All related trash will be bagged and disposed of into the jobsite dumpster provided by the Customer.
4) Color Seal Discount-
Discount applied to the total of the floor coating system. No discount is applied to additional line items or Change Orders unless approved by (Contractor Name).
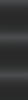
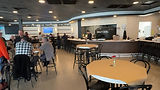
GemStone
GemStone Epoxy System-
This is a floor coating system that combines a self-leveling resin with decorative aggregate to create a monolithic coating. This innovative blend results in a floor finish that boasts glasslike flatness and exceptional durability using the methods and materials listed bellow:
1) GemStone Verify Measurements-
(Contractor Company Name) will verify the dimensions of the work area, and all details provided by the customer to create this proposal. Any additional items found to be needed or adjustments to be made, can be done as a Change Order with the approval of you the Customer.
Preparation Services
1) GemStone Coverings Removal/Demo-
If applicable remove the existing floor coverings and haul away: Tile or Carpet. Please note that if additional layers of floor coverings are found to be underneath what can be seen, a Change Order for the added cost must be made and will be based on the type and amount of additional removal needed.
2) GemStone Moisture Test-
This is a test to determine the level of moisture vapor that is naturally evaporating and outgassing from your existing concrete floor. This test does not determine any structural issues, plumbing issues, or the like. Being that all concrete floors are different, the standard acceptable results for the epoxy layers are 3 pounds of moisture per an average 1,000 square feet area, over a 24 hour period. If the results of the moisture tests are higher than the acceptable results, then we recommend a moisture vapor barrier that is listed below.
3) GemStone Diamond Grind-
Use diamond grinders around edges and as needed to achieve profile in accordance with the International Concrete Repair Institute
4) GemStone Shotblast-
A metal sand shot blaster used to achieve profile in accordance with International Concrete Repair Institute. Please note that some tooling marks from shot blasting may be visible within the coatings layers. Softer concrete surfaces may show more tooling marks than harder, newer concrete surfaces. As well, areas of weak surfaces may require additional patching, which is an unknown until after the shot blasting process has been completed. Areas that require large amounts of additional patching will require a Change Order with the approval of you the Customer.
Installation Services
1) GemStone Joint Fill-
Place backer rod into joints and install joint fill product to create a smoother surface and protect against collection water, ice, dirt and debris. Unfilled joints do not provide this protection. Note that the joints are at the surface edge in order to allow for expansion and contraction of the joint fill material.
2) GemStone Crack Fill -
Fill cracks in concrete with an epoxy patching compound. Cracks larger than 1/32" will be filled to help provide a smoother more professional appearance.
Please note that filling any crack does not create a structural repair. Epoxy creates a high-strength bond that reinforces the concrete rather than just covering the crack but does not guarantee to remediate a concrete slab that is moving, or has moisture pressure from underneath.
3) GemStone Patching-
Apply epoxy patching material to areas of concrete to reduce severity of depressions. Epoxy patching compounds are stronger than regular concrete repairs and ensure the substrate remains solid and stable under traffic and weight loads, as a properly prepped surface extends the durability and longevity of the epoxy coating.
4) GemStone Cove Base-
If purchased by the customer install an epoxy mortared cove base along the wall locations specified and at what height from the floor up the wall.
Epoxy cove bases are extremely durable in many commercial applications and help create more of a tub affect with its integral design with the floor. This helps with regular and heavy-duty cleaning processes and helps keep water from migrating under walls.
5) GemStone VaporStop-
If moisture test results are above the standard allowed by the coating material, a moisture vapor barrier is recommended. We will apply a special VaporStop coating to reduce amount of moisture that can outgas from the concrete slab and attack the coating system.
Please note that moisture vapor barriers do not protect against running water, drainage problems or the like. These coatings are intended to resist moisture vapor only and extend the life of the concrete floor.
6) GemStone Buffing/Sanding-
A rotating floor machine used to prep the surface for the next coating layer by buffing or sanding, which helps smooth out general dust and debris that naturally accumulates onto the wet epoxy layers between coats. Vacuum thoroughly once desired profile is achieved.
7) GemStone Color Layer-
Apply an approx. 1/4" of GemStone epoxy color layer. Any inconsistencies in the sub-floor, may be visible at the surface. Once cured, repeat step 6.
8) GemStone Epoxy Base Coat-
Apply 100% Solids epoxy base coat tinted in accordance with customer color information.
The epoxy base coat has excellent dwell time, rather than rapidly curing, which provides excellent penetration by seeping deep into the concrete pores, catalyzing inside the concrete and not just laying on top like paint coatings. Once cured, repeat step 6.
9) GemStone Epoxy Build Coat-
Apply a second layer of 100% epoxy, tinted in accordance with the customer color information.
The epoxy build coat helps create a thicker, stronger and smoother floor, which extends the life of the concrete coating system, is easier to clean, with a professional appearance. Once cured, repeat step 6.
10) GemStone Polyaspartic Top Coat-
Apply polyaspartic top coat tinted in accordance with customer color information.
The polyaspartic topcoat provides excellent resistance to many types of liquids, foods, animal waste, dirt, salt and more, and are highly resistant to UV light.
OR
10) GemStone Urethane Top Coat-
Apply Urethane coating tinted in accordance with customer color information.
-The High Wear Urethane is a very durable finish that is highly resistant to scratching. The appearance is also a low sheen with a slight surface texture.
-The Water Based Urethane uses water as the main solvent, making it less toxic and with lower volatile organic compounds. It dries significantly faster than oil-based urethane, allowing for multiple coats in a single day. Typically dries clear, preserving the natural color.
-The Moisture Cure Urethane is a coating that hardens when it absorbs moisture from the air or a surface. It cures in cold weather, can handle higher heat temperatures than most epoxies, can be spray applied wet-on-wet, has short drying times, and can be used in high humidity and other challenging environments.
11) GemStone Traction Control-
If purchased by the customer, add aggregate for traction control in accordance with "System Layers and Colors" Information. Add aggregate to create traction for a better nonskid surface. We recommend traction on all floors, although any surface can be slippery when wet. Adding traction does not completely eliminate the possibility of slips and falls. We (Contractor Name) cannot be responsible for any injury.
12) GemStone Haul Trash-
Remove all related trash from the work area and dispose of into an offsite dumpster.
AND/OR
12) GemStone Trash Disposal-
All related trash will be bagged and disposed of into the jobsite dumpster provided by the Customer.
13) GemStone Discount-
Discount applied to the total of the floor coating system. No discount is applied to additional line items or Change Orders unless approved by (Contractor Name).
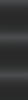
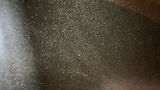
Metallika
Metallika Epoxy System-
This is a floor coating system that uses epoxy, urethane, and mica pigments to create high-end designs. It can be used in residential and commercial spaces using the methods and materials listed below:
1) Metallika Verify Measurements-
(Contractor Company Name) will verify the dimensions of the work area, and all details provided by the customer to create this proposal. Any additional items found to be needed or adjustments to be made, can be done as a Change Order with the approval of you the Customer.
Preparation Services
1) Metallika Coverings Removal/Demo-
If applicable remove the existing floor coverings and haul away: Tile or Carpet. Please note that if additional layers of floor coverings are found to be underneath what can be seen, a Change Order for the added cost must be made and will be based on the type and amount of additional removal needed.
2) Metallika Moisture Test-
This is a test to determine the level of moisture vapor that is naturally evaporating and outgassing from your existing concrete floor. This test does not determine any structural issues, plumbing issues, or the like. Being that all concrete floors are different, the standard acceptable results for the epoxy layers are 3 pounds of moisture per an average 1,000 square feet area, over a 24 hour period. If the results of the moisture tests are higher than the acceptable results, then we recommend a moisture vapor barrier that is listed below.
3) Metallika Diamond Grind-
Use diamond grinders around edges and as needed to achieve profile in accordance with the International Concrete Repair Institute.
4) Metallika Shotblast-
A metal sand shot blaster used to achieve profile in accordance with International Concrete Repair Institute. Please note that some tooling marks from shot blasting may be visible within the coatings layers. Softer concrete surfaces may show more tooling marks than harder, newer concrete surfaces. As well, areas of weak surfaces may require additional patching, which is an unknown until after the shot blasting process has been completed. Areas that require large amounts of additional patching will require a Change Order with the approval of you the Customer. Vacuum thoroughly once desired profile is achieved.
Installation Services
1) Metallika Joint Fill-
Place backer rod into joints and install joint fill product to create a smoother surface and protect against collection water, ice, dirt and debris. Unfilled joints do not provide this protection. Note that the joints are at the surface edge in order to allow for expansion and contraction of the joint fill material.
2) Metallika Crack Fill-
Fill cracks in concrete with an epoxy patching compound. Cracks larger than 1/32" will be filled to help provide a smoother more professional appearance.
Please note that filling any crack does not create a structural repair. Epoxy creates a high-strength bond that reinforces the concrete rather than just covering the crack but does not guarantee to remediate a concrete slab that is moving, or has moisture pressure from underneath.
3) Metallika Patching-
Apply epoxy patching material to areas of concrete to reduce severity of depressions. Epoxy patching compounds are stronger than regular concrete repairs and ensure the substrate remains solid and stable under traffic and weight loads, as a properly prepped surface extends the durability and longevity of the epoxy coating.
4) Metallika Cove Base-
If purchased by the customer install an epoxy mortared cove base along the wall locations specified and at what height from the floor up the wall.
Epoxy cove bases are extremely durable in many commercial applications and help create more of a tub affect with its integral design with the floor. This helps with regular and heavy-duty cleaning processes and helps keep water from migrating under walls.
5) Metallika VaporStop-
If moisture test results are above the standard allowed by the coating material, a moisture vapor barrier is recommended. We will apply a special VaporStop coating to reduce amount of moisture that can outgas from the concrete slab and attack the coating system.
Please note that moisture vapor barriers do not protect against running water, drainage problems or the like. These coatings are intended to resist moisture vapor only and extend the life of the concrete floor.
6) Metallika Buffing/Sanding-
A rotating floor machine used to prep the surface for the next coating layer by buffing or sanding, which helps smooth out general dust and debris that naturally accumulates onto the wet epoxy layers between coats. Vacuum thoroughly.
7) Metallika Epoxy Base Coat-
Apply 100% Solids epoxy base coat tinted in accordance with customer color information.
The epoxy base coat has excellent dwell time, rather than rapidly curing, which provides excellent penetration by seeping deep into the concrete pores, catalyzing inside the concrete and not just laying on top like paint coatings. Once cured, repeat step 6.
8) Metallika Polyaspartic Top Coat-
Apply polyaspartic top coat tinted in accordance with customer color information.
The polyaspartic topcoat provides excellent resistance to many types of liquids, foods, animal waste, dirt, salt and more, and are highly resistant to UV light.
OR
8) Metallika Urethane Top Coat-
Apply Urethane coating tinted in accordance with customer color information.
-The High Wear Urethane is a very durable finish that is highly resistant to scratching. The appearance is also a low sheen with a slight surface texture.
-The Water Based Urethane uses water as the main solvent, making it less toxic and with lower volatile organic compounds. It dries significantly faster than oil-based urethane, allowing for multiple coats in a single day. Typically dries clear, preserving the natural color.
-The Moisture Cure Urethane is a coating that hardens when it absorbs moisture from the air or a surface. It cures in cold weather, can handle higher heat temperatures than most epoxies, can be spray applied wet-on-wet, has short drying times, and can be used in high humidity and other challenging environments.
10) Metallika Traction Control-
If purchased by the customer, add aggregate for traction control in accordance with "System Layers and Colors" Information. Add aggregate to create traction for a better nonskid surface. We recommend traction on all floors, although any surface can be slippery when wet. Adding traction does not completely eliminate the possibility of slips and falls. We (Contractor Name) cannot be responsible for any injury.
11) Metallika Haul Trash-
Remove all related trash from the work area and dispose of into an offsite dumpster.
OR
11) Metallika Trash Disposal-
All related trash will be bagged and disposed of into the jobsite dumpster provided by the Customer.
12) Metallika Discount-
Discount applied to the total of the floor coating system. No discount is applied to additional line items or Change Orders unless approved by (Contractor Name).
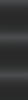

Mosaic Flake
Mosaic Flake Epoxy System-
This system uses a vinyl flake, sandwiched between a base coat of wet resin and at least one clear topcoat. This system is known for it's durability and longevity a multicolored decorative appearance with the use of flakes allows for a wide range of colors and patterns, using the methods and materials listed below:
1) Mosaic Flake Verify Measurements-
(Contractor Company Name) will verify the dimensions of the work area, and all details provided by the customer to create this proposal. Any additional items found to be needed or adjustments to be made, can be done as a Change Order with the approval of you the Customer.
Preparation Services
1) Mosaic Flake Coverings Removal/Demo-
If applicable remove the existing floor coverings and haul away: Tile or Carpet. Please note that if additional layers of floor coverings are found to be underneath what can be seen, a Change Order for the added cost must be made and will be based on the type and amount of additional removal needed.
2) Mosaic Flake Moisture Test-
This is a test to determine the level of moisture vapor that is naturally evaporating and outgassing from your existing concrete floor. This test does not determine any structural issues, plumbing issues, or the like. Being that all concrete floors are different, the standard acceptable results for the epoxy layers are 3 pounds of moisture per an average 1,000 square feet area, over a 24 hour period. If the results of the moisture tests are higher than the acceptable results, then we recommend a moisture vapor barrier that is listed below.
3) Mosaic Flake Diamond Grind-
Use diamond grinders around edges and as needed to achieve profile in accordance with the International Concrete Repair Institute
4) Mosaic Flake Shotblast-
A metal sand shot blaster used to achieve profile in accordance with International Concrete Repair Institute. Please note that some tooling marks from shot blasting may be visible within the coatings layers. Softer concrete surfaces may show more tooling marks than harder, newer concrete surfaces. As well, areas of weak surfaces may require additional patching, which is an unknown until after the shot blasting process has been completed. Areas that require large amounts of additional patching will require a Change Order with the approval of you the Customer. Vacuum thoroughly.
Installation Services
1) Mosaic Flake Joint Fill-
Place backer rod into joints and install joint fill product to create a smoother surface and protect against collection water, ice, dirt and debris. Unfilled joints do not provide this protection. Note that the joints are at the surface edge in order to allow for expansion and contraction of the joint fill material.
2) Mosaic Flake Crack Fill -
Fill cracks in concrete with an epoxy patching compound. Cracks larger than 1/32" will be filled to help provide a smoother more professional appearance.
Please note that filling any crack does not create a structural repair. Epoxy creates a high-strength bond that reinforces the concrete rather than just covering the crack but does not guarantee to remediate a concrete slab that is moving, or has moisture pressure from underneath.
3) Mosaic Flake Patching-
Apply epoxy patching material to areas of concrete to reduce severity of depressions. Epoxy patching compounds are stronger than regular concrete repairs and ensure the substrate remains solid and stable under traffic and weight loads, as a properly prepped surface extends the durability and longevity of the epoxy coating.
4) Mosaic Flake Cove Base-
If purchased by the customer install an epoxy mortared cove base along the wall locations specified and at what height from the floor up the wall.
Epoxy cove bases are extremely durable in many commercial applications and help create more of a tub affect with its integral design with the floor. This helps with regular and heavy-duty cleaning processes and helps keep water from migrating under walls.
5) Mosaic Flake VaporStop-
If moisture test results are above the standard allowed by the coating material, a moisture vapor barrier is recommended. We will apply a special VaporStop coating to reduce amount of moisture that can outgas from the concrete slab and attack the coating system.
Please note that moisture vapor barriers do not protect against running water, drainage problems or the like. These coatings are intended to resist moisture vapor only and extend the life of the concrete floor.
6) Mosaic Flake Buffing/Sanding-
A rotating floor machine used to prep the surface for the next coating layer by buffing or sanding, which helps smooth out general dust and debris that naturally accumulates onto the wet epoxy layers between coats. Vacuum thoroughly.
7) Mosaic Flake Epoxy Base Coat-
Apply 100% Solids epoxy base coat tinted in accordance with customer color information.
The epoxy base coat has excellent dwell time, rather than rapidly curing, which provides excellent penetration by seeping deep into the concrete pores, catalyzing inside the concrete and not just laying on top like paint coatings.
9) Mosaic Flake Broadcast-
Apply a full broadcast of the Mosaic Flake in the size and color blend as indicated in the "System Layers and Colors" information. After cured use floor scraper to knock down high spots and sharp flakes.
10) Mosaic Flake Polyaspartic Top Coat-
Apply polyaspartic top coat tinted in accordance with customer color information.
The polyaspartic topcoat provides excellent resistance to many types of liquids, foods, animal waste, dirt, salt and more, and are highly resistant to UV light.
11) Mosaic Flake Traction Control-
If purchased by the customer, add aggregate for traction control in accordance with "System Layers and Colors" Information. Add aggregate to create traction for a better nonskid surface. We recommend traction on all floors, although any surface can be slippery when wet. Adding traction does not completely eliminate the possibility of slips and falls. We (Contractor Name) cannot be responsible for any injury.
12) Mosaic Flake Haul Trash-
Remove all related trash from the work area and dispose of into an offsite dumpster.
OR
12) Mosaic Flake Trash Disposal-
All related trash will be bagged and disposed of into the jobsite dumpster provided by the Customer.
13) Mosaic Flake Discount-
Discount applied to the total of the floor coating system. No discount is applied to additional line items or Change Orders unless approved by (Contractor Name).
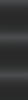

Polish & Seal
Polish & Seal System-
This is a process beginning with grinding the concrete surface using progressively finer diamond tooling to improve the smoothness, hardness and increase its sheen, followed by applying a sealer to protect it and enhance its appearance using the methods and materials listed below:
1) Polish & Seal Verify Measurements-
(Contractor Company Name) will verify the dimensions of the work area, and all details provided by the customer to create this proposal. Any additional items found to be needed or adjustments to be made, can be done as a Change Order with the approval of you the Customer.
Preparation Services
1) Polish & Seal Hardness Check-
Check the hardness of the concrete to be polished and qualify that the process can be done with the condition of the concrete.
2) Polish & Seal Diamond Grind-
Use diamond grinders as needed to achieve profile in accordance with the International Concrete Repair Institute
Installation Services
1) Polish & Seal Densifier-
Apply concrete densifier
2) Polish & Seal Sealing -
Apply sealer to the concrete in accordance with the "System Layers and Colors" Information
3) Polish & Seal Burnish-
Burnish to activate sealer
4) Polish & Seal Haul Trash-
Remove all related trash from the work area and dispose of into an offsite dumpster.
OR
4) Polish & Seal Trash Disposal-
All related trash will be bagged and disposed of into the jobsite dumpster provided by the Customer.
5) Polish & Seal Discount-
Discount applied to the total of the floor coating system. No discount is applied to additional line items or Change Orders unless approved by (Contractor Name).
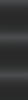

Stamped Overlay
Stamped Overlay System-
This is a decorative technique where a thin layer of concrete, known as concrete overlay, is applied over an existing concrete surface, which is then stamped to create a textured, visually appealing finish using the methods and materials bellow:
1) Stamped Overlay Verify Measurements-
(Contractor Company Name) will verify the dimensions of the work area, and all details provided by the customer to create this proposal. Any additional items found to be needed or adjustments to be made, can be done as a Change Order with the approval of you the Customer.
Preparation Services
1) Stamped Overlay Power Wash-
Power wash the concrete surface.
2) Stamped Overlay Shotblast-
A metal sand shot blaster used to achieve profile in accordance with International Concrete Repair Institute. Please note that some tooling marks from shot blasting may be visible within the coatings layers. Softer concrete surfaces may show more tooling marks than harder, newer concrete surfaces. As well, areas of weak surfaces may require additional patching, which is an unknown until after the shot blasting process has been completed. Areas that require large amounts of additional patching will require a Change Order with the approval of you the Customer.
3) Stamped Overlay Diamond Grind-
Use diamond grinders around edges and as needed to achieve profile in accordance with the International Concrete Repair Institute. Vacuum thoroughly once desired profile os achieved.
4) Stamped Overlay Patching-
Apply patching material to areas of concrete to reduce severity of depressions. Unless measured, amount of patching material will be determined on-site and may result in a Change Order
5) Stamped Overlay Primer Coat-
Concrete primer to be applied before overlay.
Installation Services
1) Stamped Overlay Base Coat-
Trowel a base coat of overlay
2) Stamped Overlay Top Coat -
Trowel a top coat of concrete overlay. Apply an engineered concrete overlay in accordance with the "System Layers and Colors" Information
3) Stamped Overlay Pattern/Texture-
Pattern: Apply a stamped concrete overlay using a pattern stamp in accordance with the "System Layers and Colors" Information
Texture: Apply a stamped concrete overlay using a texture, no pattern, in accordance with the "System Layers and Colors" Information
4) Stamped Overlay Antiquing-
If purchased by the customer, apply antique decorative wash.
5) Stamped Overlay Grout-
If purchased by the customer, apply grout material in accordance with the "System Layers and Colors" Information
6) Stamped Overlay Sealer-
Apply sealer to the overlay system in accordance with the "System Layers and Colors" Information
7) Stamped Overlay Traction-
If purchased by the customer, add aggregate for traction control in accordance with "System Layers and Colors" Information. Add aggregate to create traction for a better nonskid surface. We recommend traction on all floors, although any surface can be slippery when wet. Adding traction does not completely eliminate the possibility of slips and falls. We (Contractor Name) cannot be responsible for any injury.
8) Stamped Overlay Haul Trash-
Remove all related trash from the work area and dispose of into an offsite dumpster.
OR
8) Stamped Overlay Trash Disposal-
All related trash will be bagged and disposed of into the jobsite dumpster provided by the Customer.
9) Stamped Overlay Discount-
Discount applied to the total of the floor coating system. No discount is applied to additional line items or Change Orders unless approved by (Contractor Name).
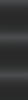

Urethane
Urethane System-
This is a type of floor coating made from a thermosetting polymer, polyurethane, that is applied to concrete floors to create a durable, seamless, and waterproof surface offering resistance to chemicals, abrasion, and long term wear. It is often used in commercial spaces for its hygienic and easy-to-clean properties, applied using the methods and materials listed below:
1) Urethane Verify Measurements-
(Contractor Company Name) will verify the dimensions of the work area, and all details provided by the customer to create this proposal. Any additional items found to be needed or adjustments to be made, can be done as a Change Order with the approval of you the Customer.
Preparation Services
1) Urethane Coverings Removal/Demo-
If applicable remove the existing floor coverings and haul away: Tile or Carpet.
Please note that if additional layers of floor coverings are found to be underneath what can be seen, a Change Order for the added cost must be made and will be based on the type and amount of additional removal needed.
2) Urethane Moisture Test-
This is a test to determine the level of moisture vapor that is naturally evaporating and outgassing from your existing concrete floor. This test does not determine any structural issues, plumbing issues, or the like. Being that all concrete floors are different, the standard acceptable results for the epoxy layers are 3 pounds of moisture per an average 1,000 square feet area, over a 24 hour period. If the results of the moisture tests are higher than the acceptable results, then we recommend a moisture vapor barrier that is listed below.
3) Urethane Diamond Grind-
Use diamond grinders around edges and as needed to achieve profile in accordance with the International Concrete Repair Institute
4) Urethane Shotblast-
A metal sand shot blaster used to achieve profile in accordance with International Concrete Repair Institute. Please note that some tooling marks from shot blasting may be visible within the coatings layers. Softer concrete surfaces may show more tooling marks than harder, newer concrete surfaces. As well, areas of weak surfaces may require additional patching, which is an unknown until after the shot blasting process has been completed. Areas that require large amounts of additional patching will require a Change Order with the approval of you the Customer. Vacuum thoroughly once desired profile is achieved.
5) Urethane Patching-
Apply patching material to areas of concrete to reduce severity of depressions. Unless measured, amount of patching material will be determined on-site and may result in a Change Order
Installation Services
1) Urethane Cove Base-
If purchased by the customer install an epoxy mortared cove base along the wall locations specified and at what height from the floor up the wall.
Epoxy cove bases are extremely durable in many commercial applications and help create more of a tub affect with its integral design with the floor. This helps with regular and heavy-duty cleaning processes and helps keep water from migrating under walls.
2) Urethane Self Leveling Mortar-
Apply a self leveling urethane mortar to an approximate thickness of 1/4" to 3/8" thick.
3) Urethane Mortar Sand -
Broadcast sand into the surface of leveler to increase thickness and strength and provide slip resistant surface
4) Urethane Top Coat-
Apply top coat of high wear urethane in accordance with "System Layers & Colors" information
5) Urethane Finish Coat-
Apply a final finish of a urethane coating. The sheen of the urethane coating is to be determined prior to the start of the job. If no specifics have been made, (Contractor Name) will use their discretion as to the final level of sheen.
6) Urethane Traction-
If purchased by the customer, add aggregate for traction control in accordance with "System Layers and Colors" Information. Add aggregate to create traction for a better nonskid surface. We recommend traction on all floors, although any surface can be slippery when wet. Adding traction does not completely eliminate the possibility of slips and falls. We (Contractor Name) cannot be responsible for any injury.
7) Urethane Haul Trash-
Remove all related trash from the work area and dispose of into an offsite dumpster.
OR
7) Urethane Trash Disposal-
All related trash will be bagged and disposed of into the jobsite dumpster provided by the Customer.
8) Urethane Discount-
Discount applied to the total of the floor coating system. No discount is applied to additional line items or Change Orders unless approved by (Contractor Name).
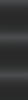

Solid Sands
1) Solid Sands System-
This is a system of epoxy and urethane layers that utilizes the strength and durability of embedded natural quartz sand. Applied using the methods and materials listed below:
2) Solid Sands Verify Measurements-
(Contractor Company Name) will verify the dimensions of the work area, and all details provided by the customer to create this proposal. Any additional items found to be needed or adjustments to be made, can be done as a Change Order with the approval of you the Customer.
Preparation Services
1) Solid Sands Coverings Removal/Demo-
If applicable remove the existing floor coverings and haul away: Tile or Carpet. Please note that if additional layers of floor coverings are found to be underneath what can be seen, a Change Order for the added cost must be made and will be based on the type and amount of additional removal needed.
2) Solid Sands Moisture Test-
This is a test to determine the level of moisture vapor that is naturally evaporating and outgassing from your existing concrete floor. This test does not determine any structural issues, plumbing issues, or the like. Being that all concrete floors are different, the standard acceptable results for the epoxy layers are 3 pounds of moisture per an average 1,000 square feet area, over a 24 hour period. If the results of the moisture tests are higher than the acceptable results, then we recommend a moisture vapor barrier that is listed below.
3) Solid Sands Diamond Grind-
Use diamond grinders around edges and as needed to achieve profile in accordance with the International Concrete Repair Institute
4) Solid Sands Shotblast-
A metal sand shot blaster used to achieve profile in accordance with International Concrete Repair Institute. Please note that some tooling marks from shot blasting may be visible within the coatings layers. Softer concrete surfaces may show more tooling marks than harder, newer concrete surfaces. As well, areas of weak surfaces may require additional patching, which is an unknown until after the shot blasting process has been completed. Areas that require large amounts of additional patching will require a Change Order with the approval of you the Customer.
Installation Services
1) Solid Sands Joint Fill-
Place backer rod into joints and install joint fill product to create a smoother surface and protect against collection water, ice, dirt and debris. Unfilled joints do not provide this protection. Note that the joints are at the surface edge in order to allow for expansion and contraction of the joint fill material.
2) Solid Sands Crack Fill -
Fill cracks in concrete with an epoxy patching compound. Cracks larger than 1/32" will be filled to help provide a smoother more professional appearance.
Please note that filling any crack does not create a structural repair. Epoxy creates a high-strength bond that reinforces the concrete rather than just covering the crack but does not guarantee to remediate a concrete slab that is moving, or has moisture pressure from underneath.
3) Solid Sands Patching-
Apply epoxy patching material to areas of concrete to reduce severity of depressions. Epoxy patching compounds are stronger than regular concrete repairs and ensure the substrate remains solid and stable under traffic and weight loads, as a properly prepped surface extends the durability and longevity of the epoxy coating.
4) Solid Sands Cove Base-
If purchased by the customer install an epoxy mortared cove base along the wall locations specified and at what height from the floor up the wall.
Epoxy cove bases are extremely durable in many commercial applications and help create more of a tub affect with its integral design with the floor. This helps with regular and heavy-duty cleaning processes and helps keep water from migrating under walls.
5) Solid Sands VaporStop-
If moisture test results are above the standard allowed by the coating material, a moisture vapor barrier is recommended. We will apply a special VaporStop coating to reduce amount of moisture that can outgas from the concrete slab and attack the coating system.
Please note that moisture vapor barriers do not protect against running water, drainage problems or the like. These coatings are intended to resist moisture vapor only and extend the life of the concrete floor.
6) Solid Sands Epoxy Base Coat-
Apply 100% Solids epoxy base coat tinted in accordance with customer color information.
The epoxy base coat has excellent dwell time, rather than rapidly curing, which provides excellent penetration by seeping deep into the concrete pores, catalyzing inside the concrete and not just laying on top like paint coatings.
7) Solid Sands Epoxy Build Coat-
Apply a second layer of 100% epoxy, tinted in accordance with the customer color information.
The epoxy build coat helps create a thicker, stronger and smoother floor, which extends the life of the concrete coating system, is easier to clean, with a professional appearance.
8) Solid Sands Broadcast-
Apply a full broadcast of the quartz sand in the size and color blend as indicated in the "System Layers and Colors" information.
9) Solid Sands Polyaspartic Build Coat-
Apply a polyaspartic layer as build coat in accordance with "System Layers & Colors" information
The polyaspartic build coat helps create a thicker, stronger and smoother floor, which extends the life of the concrete coating system, is easier to clean, with a professional appearance.
10) Solid Sands Polyaspartic Top Coat-
Apply polyaspartic top coat tinted in accordance with customer color information.
The polyaspartic topcoat provides excellent resistance to many types of liquids, foods, animal waste, dirt, salt and more, and are highly resistant to UV light.
11) Solid Sands Traction Control-
If purchased by the customer, add aggregate for traction control in accordance with "System Layers and Colors" Information. Add aggregate to create traction for a better nonskid surface. We recommend traction on all floors, although any surface can be slippery when wet. Adding traction does not completely eliminate the possibility of slips and falls. We (Contractor Name) cannot be responsible for any injury.
12) Solid Sands Haul Trash-
Remove all related trash from the work area and dispose of into an offsite dumpster.
OR
12) Solid Sands Trash Disposal-
All related trash will be bagged and disposed of into the jobsite dumpster provided by the Customer.
13) Solid Sands Discount-
Discount applied to the total of the floor coating system. No discount is applied to additional line items or Change Orders unless approved by (Contractor Name).
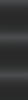

Concrete Self Leveler
1) Concrete Self Leveler System-
This is a polymer-modified cement mixture that flows easily and sets quickly, allowing it to semi self level to create a smoother, flater surface for flooring installation. Applied using the methods and materials listed below:
2) Concrete Self Leveler Verify Measurements-
(Contractor Company Name) will verify the dimensions of the work area, and all details provided by the customer to create this proposal. Any additional items found to be needed or adjustments to be made, can be done as a Change Order with the approval of you the Customer.
Preparation Services
1) Concrete Self Leveler Power Wash-
Power wash the concrete surface.
2) Concrete Self Leveler Patching-
Apply patching material to areas of concrete to reduce severity of depressions. Unless measured, amount of patching material will be determined on-site and may result in a Change Order
3) Concrete Self Leveler Primer Coat-
Concrete primer to be applied before overlay.
4) Concrete Self Leveler Shotblast-
A metal sand shot blaster used to achieve profile in accordance with International Concrete Repair Institute. Please note that some tooling marks from shot blasting may be visible within the coatings layers. Softer concrete surfaces may show more tooling marks than harder, newer concrete surfaces. As well, areas of weak surfaces may require additional patching, which is an unknown until after the shot blasting process has been completed. Areas that require large amounts of additional patching will require a Change Order with the approval of you the Customer.
Installation Services
1) Concrete Self Leveler Base Coat-
Trowel a base coat of overlay
2) Concrete Self Leveler Top Coat -
Trowel a top coat of concrete overlay. Apply an engineered concrete overlay in accordance with the "System Layers and Colors" Information
3) Concrete Self Leveler Pattern/Texture-
Pattern: Apply a stamped concrete overlay using a pattern stamp in accordance with the "System Layers and Colors" Information
Texture: Apply a stamped concrete overlay using a texture, no pattern, in accordance with the "System Layers and Colors" Information
4) Concrete Self Leveler Border-
If purchased by the customer, apply an Overlay border in accordance with the "System Layers and Colors" Information
5) Concrete Self Leveler Antiquing-
If purchased by the customer, apply antique decorative wash.
6) Concrete Self Leveler Sealer-
Apply sealer to the overlay system in accordance with the "System Layers and Colors" Information
7) Concrete Self Leveler Traction-
Add aggregate for traction control in accordance with "System Layers and Colors" Information. Add aggregate to create traction for a better nonskid surface. We recommend traction on all floors, although any surface can be slippery when wet. Adding traction does not completely eliminate the possibility of slips and falls. We (Contractor Name) cannot be responsible for any injury.
8) Concrete Self Leveler Haul Trash-
Remove all related trash from the work area and dispose of into an offsite dumpster.
9) Concrete Self Leveler Trash Disposal-
All related trash will be bagged and disposed of into the jobsite dumpster provided by the Customer.
10) Concrete Self Leveler Discount-
Discount applied to the total of the floor coating system. No discount is applied to additional line items or Change Orders unless approved by (Contractor Name).